Toyota Reports 80-Percent Decrease in Acceleration Complaints
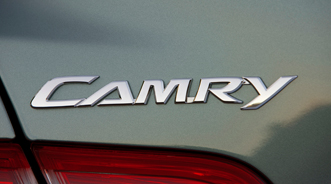
Toyota Motor Engineering and Manufacturing North America said Monday that it has seen an 80-percent decrease in reports of acceleration-related concerns from customers since April when its SMART evaluation program was rolled out.
With these efforts to address acceleration-related issues being so successful, TEMA said its SMART program will be enlarged to tackle other areas of customer concern that may come up.
Also, the company revealed that more than 5 million fixes under three recalls have been completed (sticking accelerator pedals, floor-mat issues, anti-lock brake systems).
"Since its launch, the SMART process has evaluated approximately 4,200 vehicles, giving Toyota a better understanding of what customers are actually experiencing. Importantly, Toyota has not found a single case in which the vehicle’s electronic throttle control system would lead to unintended acceleration," officials highlighted.
“This utilization of the SMART portfolio is intended to further strengthen the company’s field information gathering and evaluation capabilities as well as its ability to respond quickly to the needs of its customers,” Toyota management said in a statement released Monday.
Steve St. Angelo, the automaker’s North American chief quality officer, attended a news briefing with Rodney Slater, a former U.S. Secretary of Transportation and chairman of the Toyota’s independent North American Quality Advisory Panel.
“Toyota has made significant progress in recent months to help ensure that our customers can have complete confidence in the quality, safety and reliability of their vehicles, and our latest initiatives build on those accomplishments,” St. Angelo said. “Toyota’s continuous efforts to strengthen vehicle quality and safety, and to respond swiftly and thoroughly to our customers’ concerns, are driven by our core values and will always be a fundamental part of our company.
“Our goal is to set new, even higher standards for quality assurance and customer responsiveness in both the factory and the market by continuing to put our customers first in everything that we do,” St. Angelo added.
The companyalso said it is increasing the frequency of reliability testing of key parts, such as more frequent evaluation of parts to confirm functionality and identify any damage sustained during shipment.
Toyota said it is also working more closely with suppliers at the beginning of the development and design process so that Toyota’s expectations and quality criteria for key parts are clearly communicated.
"In order to benefit from the knowledge and experience of its suppliers, Toyota is revising its Supplier Quality Assurance Manual to capture supplier best practices, benchmarks of global competitors, and other feedback from Toyota’s supplier review. Toyota’s North American Center for Quality Excellence will also expand its curriculum in the near future to include training for suppliers in Toyota Quality and Design activities, best practice sharing and new quality assurance," management pointed out.
In addition to sharing the strong results and expansion of SMART, St. Angelo revealed the following quality leadership initiatives:
—Toyota plans to add more safety features into all of its new vehicles. These include Smart Stop Technology and enhanced data recorders.
—The automaker is bringing new procedures regarding training with the aim of bolstering its lineup’s quality, safety and reliability even more. Toyota is also doing this to be able to respond to customer needs better.
—Toyota is teaming up with suppliers so that systems already in place can be improved and that it can ensure “best practices across the supply chain.” Manufacturing processes, quality assurance policies and testing procedures for key parts are being evaluated.