GM details ‘rapid response’ face mask project
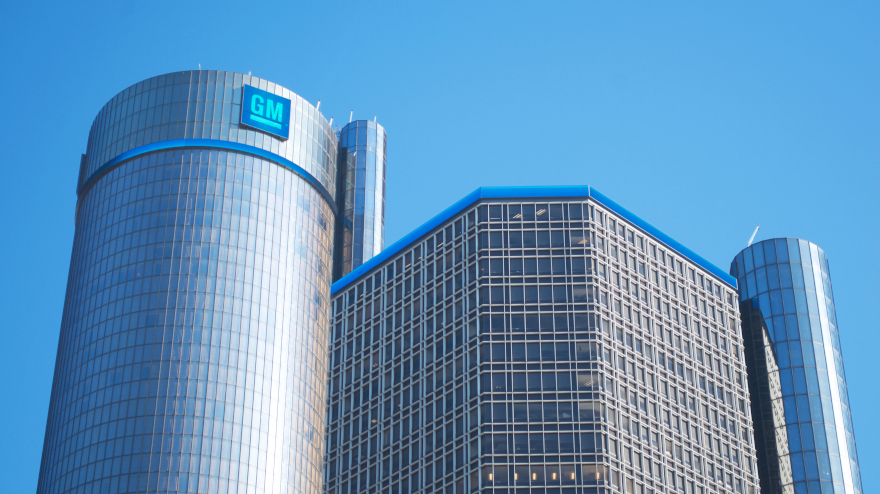
Editorial credit: Linda Parton / Shutterstock.com
With the spread of COVID-19, General Motors says it has sought to use its talents and resources to help in the shared fight against the pandemic.
The pandemic created a shortage of face masks, and GM on March 20 launched what it described as a “rapid-response project” to produce masks at scale to help protect workers in essential services across the country.
“Working around the clock, our team rallied with incredible passion and focus to come up with a plan to produce masks that will help protect the women and men on the front lines of this crisis.” said GM vice president, global manufacturing engineering, Peter Thom, in a news release.
GM says it launched a rapid-response project on March 20 to produce masks at scale.
Seven days later, the team produced its first sample on the new production line.
On Tuesday, GM said that it expects to deliver its first 20,000 masks to frontline workers by next week.
The company said that the project would have taken several months to plan and execute without help from its partners around the globe. GM said the team working on the face-mask project accomplished the task in just one week.
GM asked more than 30 engineers, designers, buyers and members of the manufacturing team to help with product development, sourcing materials and equipment, and planning the production process.
The company first called those who work with fabric vehicle components, said Karsten Garbe, who is GM plant director, global pre-production operations.
“In a few days, the company’s seat belt and interior trim experts became experts in manufacturing face masks,” Garbe said in a news release.
The team used its existing supply chain to source the necessary raw materials. Those materials include metal nose pieces, elastic straps and blown, non-woven fabric filter material.
To design and build the custom machinery needed to assemble the masks, GM collaborated with JR Automation in Holland, Mich. and Esys Automation in Auburn Hills.
For the project, the team chose the ISO Class 8-equivalent cleanroom at GM’s manufacturing plant in Warren. Crews installed new electrical service lines to power the production equipment and assembly stations.
Crews installed equipment and staged the production line, testing each step in the production process and looking for opportunities to improve quality and production speed.
The project team had its first production-made mask on Friday.
“Not only did the team make their goal, but they over-delivered,” Thom said.
Thom added, “They actually beat our deadline, running the first mask through the equipment 30 minutes ahead of target. We’re excited because this means we’re even closer to being able to protect the healthcare teams who are working tirelessly to save lives.”
Teams working through the weekend produced more than 2,000 masks by Monday.
These initial test samples will be used to ensure the quality standards are met. After completion of those quality measures, the team could begin producing masks for delivery early next week.
To staff mask operations, GM and the UAW will seek more than two dozen paid volunteers from Detroit-area plants. GM has implemented safety measures to protect those team members, including physical distancing, enhanced on-site cleaning and pre-entry health screening.
The team expects to have 20,000 masks ready for delivery on April 8.
GM says it will be able to produce up to 50,000 masks every day — or up to 1.5 million masks a month — once the line is running at full speed.
The company is planning distribution of the masks, and those plans include use of safety equipment to protect employees.
GM has posted information on its efforts to combat the COVID-19 outbreak at https://www.gm.com/coronavirus.html.